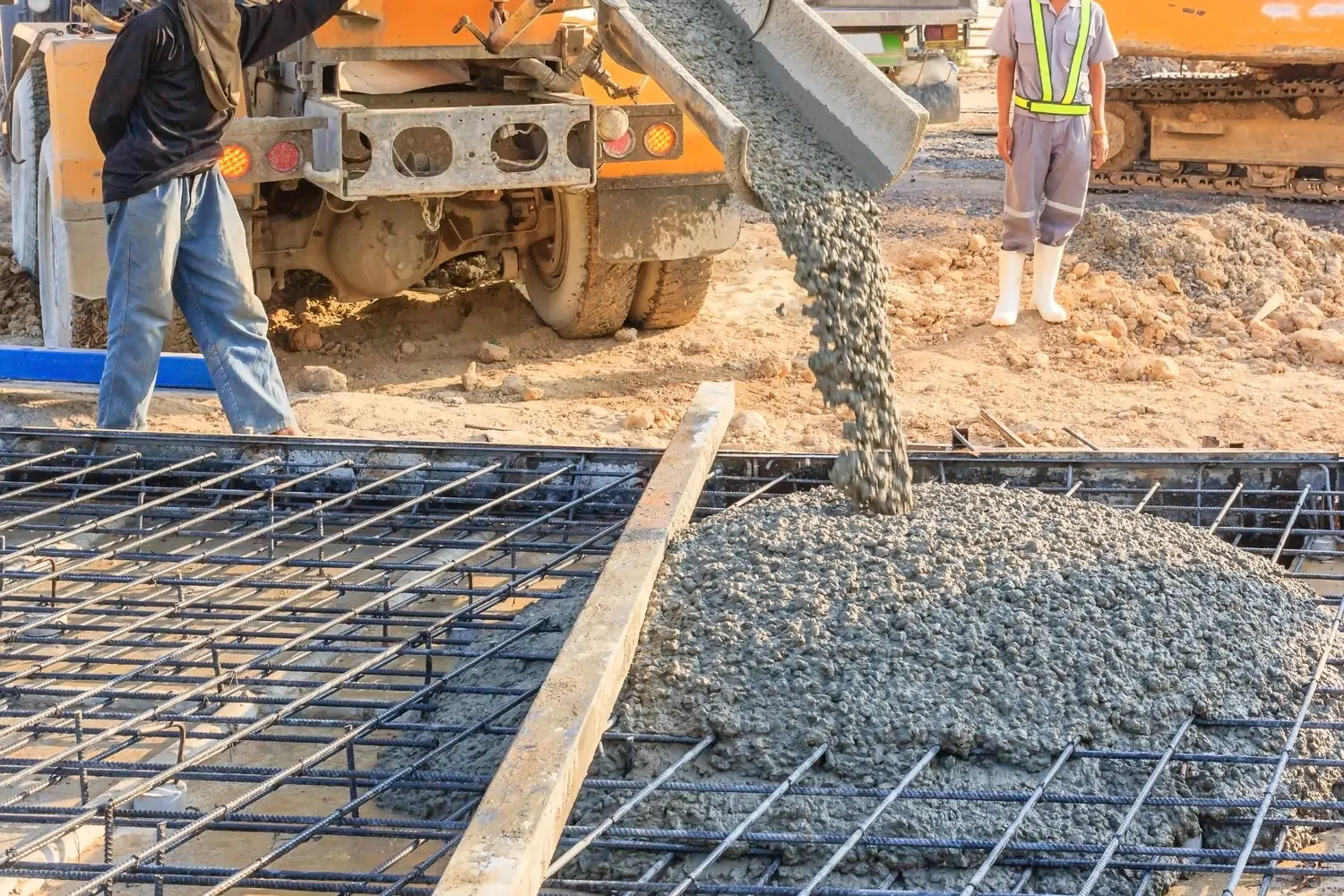
Have you ever wondered how the strength and durability of concrete structures are achieved? The secret lies in the use of rebar, or reinforcing bar, which is essential for enhancing concrete’s tensile strength.
Understanding rebar sizes, grades, and types is important for anyone involved in construction or engineering, as it directly impacts the integrity and longevity of a structure.
Whether you’re a seasoned professional pouring the foundation for a large building or a DIYer looking to make their soon-to-be patio stronger, knowing the right rebar for your project can make all the difference.
In this comprehensive guide, we’ll break down the complexities of rebar specifications, helping you choose the right materials for your project needs. By the end, you’ll have a clear understanding of rebar characteristics and how to apply them effectively, ensuring your projects are both safe and well put together.
Let’s get to it!
What Is Rebar?
Rebar, short for reinforcing bar, is a steel bar or mesh of steel wires used to reinforce and strengthen concrete structures.
Concrete is strong in compression but weak in tension; rebar compensates for this weakness by providing tensile strength, making the overall structure more durable and resilient.
Typically made from carbon steel, rebar features surface deformations or ridges to improve its bond with concrete. These ridges ensure that the rebar remains securely embedded within the concrete, preventing slippage and enhancing the structure's integrity.
Rebar comes in various sizes, grades, and types, each suited for specific applications and construction needs. The selection of the appropriate rebar is important, as it directly affects the load-bearing capacity and stability of the structure.
From small residential projects to large-scale commercial and industrial ones, rebar plays its part in ensuring that concrete can withstand various stresses and environmental conditions.
Rebar Size Chart
Different countries have their own way of measuring rebar. Below, we break down the 3 most common: U.S., European and Canadian.
U.S
U.S. rebar sizes are denoted using a number system that represents the nominal diameter of the rebar in eighths of an inch. Here’s a breakdown of what these numbers mean and how they relate:
- Bar Number: In the U.S. rebar size chart, rebar is identified by a bar number. This number corresponds to the rebar’s nominal diameter in eighths of an inch. For example, a #4 rebar has a nominal diameter of 4/8 inch (or 1/2 inch), and a #8 rebar has a nominal diameter of 8/8 inch (or 1 inch).
- Nominal Diameter: The bar number directly translates to the nominal diameter in eighths of an inch. Understanding this conversion is crucial for determining the rebar’s size and application. Larger bar numbers indicate a greater diameter, which corresponds to increased strength and load-bearing capacity.
- Cross-Sectional Area: The nominal diameter also relates to the rebar’s cross-sectional area. A larger diameter results in a larger cross-sectional area, providing more reinforcement and support to concrete structures. This is a key factor in structural design, as it affects the overall strength and stability of the construction.
- Weight: Rebar is often sold by weight, which is determined by the diameter and length. Knowing the bar number helps in calculating the weight of the rebar needed for a project. For instance, a #4 rebar will weigh less per foot compared to a #8 rebar.
European
European rebar sizes are typically expressed in millimeters (mm) and indicate the nominal diameter of the rebar. Here’s a breakdown of what these numbers mean and how they relate:
- Nominal Diameter: The numbers in the chart represent the nominal diameter of the rebar in millimeters. For example, a rebar labeled as "12" has a nominal diameter of 12 mm. This diameter is crucial as it determines the rebar’s strength and suitability for different types of construction projects.
- Cross-Sectional Area: The nominal diameter correlates with the cross-sectional area of the rebar, which is a critical factor in determining its load-bearing capacity. Larger diameters indicate a greater cross-sectional area, providing more strength and support to the concrete structure.
- Weight: The size also affects the weight of the rebar. Rebar is typically sold by weight, and knowing the diameter helps in calculating the total weight required for a project. The weight per meter of rebar increases with the diameter, meaning thicker bars will weigh more per unit length.
Canadian
Canadian rebar sizes are denoted using a number system that relates to the nominal diameter of the rebar in millimeters. Here’s a breakdown n of what these numbers mean and how they relate:
- Bar Number: In the Canadian rebar size chart, rebar is identified by a bar number, which corresponds to its nominal diameter in millimeters. For example, a rebar labeled as "15M" has a nominal diameter of approximately 15 millimeters.
- Nominal Diameter: The bar number indicates the nominal diameter of the rebar in millimeters. This measurement is crucial for determining the rebar’s size and its appropriate applications in construction projects. For instance, a "10M" rebar has a nominal diameter of about 10 millimeters.
- Cross-Sectional Area: The nominal diameter directly affects the cross-sectional area of the rebar, which is a key factor in its load-bearing capacity. Larger diameters correspond to greater cross-sectional areas, providing more reinforcement and support to concrete structures. This relationship is essential for structural engineers when designing reinforced concrete elements.
- Weight: Rebar is typically sold by weight, which is influenced by its diameter and length. Understanding the bar number helps in calculating the total weight required for a project. For example, a "20M" rebar will weigh more per meter than a "10M" rebar due to its larger diameter.
Common Use-Cases
- #3 — This thin, low-cost steel rebar is primarily used in light-duty construction projects such as residential foundations, driveways, sidewalks and pools.
- #4 — A bit thicker than #3, #4 rebar is commonly used in medium to heavy-duty construction projects such as large residential foundations, industrial floors, and retaining walls.
- #5 — This size is typically used in heavy-duty construction projects such as bridge decks, highway pavement, and large-scale commercial buildings.
- #6 — Used in heavy construction projects such as high-rise buildings, parking structures, and major infrastructure projects like bridges and dams.
- #7 — Used in heavy-duty construction projects such as industrial buildings, large-scale bridges, and infrastructure projects requiring high structural strength and durability.
- #8 — Used in extremely heavy-duty construction projects such as high-rise buildings, large-scale bridges, and industrial structures where maximum load-bearing capacity is required.
- #9 — Used in exceptionally heavy-duty construction projects such as massive industrial structures, large-scale infrastructure projects, and specialized applications requiring extreme load-bearing capacity and structural reinforcement.
- #10 — Basically the same as #9!
- #11 — Used in specialized construction projects that require extremely high load-bearing capacity and structural reinforcement, such as large-scale infrastructure and specialized engineering projects.
- #14 — Basically the same as #11!
- #18 — The largest type of rebar. Used for projects that require the most strength and durability.
Rebar Grades
Rebar grades refer to the standard specifications that define the mechanical properties and characteristics of reinforcing bars used in construction. These grades are typically designated by numbers or letters and indicate the yield strength of the rebar, which is the amount of stress at which the rebar will deform permanently. The most common rebar grades used in construction include:
- Grade 40 (300 MPa): This grade of rebar has a minimum yield strength of 40,000 pounds per square inch (or 300 megapascals). Grade 40 rebar is commonly used in light to moderate load-bearing applications, such as residential construction and low-rise buildings.
- Grade 60 (420 MPa): Grade 60 rebar has a minimum yield strength of 60,000 pounds per square inch (or 420 megapascals). It is one of the most widely used grades of rebar and is suitable for a variety of applications, including medium to heavy load-bearing structures such as bridges, highways, and commercial buildings.
- Grade 75 (520 MPa): Grade 75 rebar has a minimum yield strength of 75,000 pounds per square inch (or 520 megapascals). It offers higher strength than Grade 60 rebar and is often used in applications where increased strength and durability are required, such as high-rise buildings, parking garages, and industrial facilities.
- Grade 80 (550 MPa): Grade 80 rebar has a minimum yield strength of 80,000 pounds per square inch (or 550 megapascals). It is a high-strength rebar grade suitable for demanding applications where superior strength and performance are essential, such as heavy industrial structures and earthquake-resistant buildings.
- Grade 100 (690 MPa): Grade 100 rebar has a minimum yield strength of 100,000 pounds per square inch (or 690 megapascals). It is the highest-strength rebar grade available and is used in specialized applications where extreme strength and durability are required, such as high-rise buildings, bridges, and infrastructure projects subjected to heavy loads or seismic forces.
These rebar grades are standardized by organizations such as ASTM International (American Society for Testing and Materials) and ACI (American Concrete Institute) to ensure consistency and quality in construction materials. The selection of the appropriate rebar grade depends on factors such as the structural design, intended use, and environmental conditions of the project.
Rebar Types — Characteristics, Applications and Limitations
Carbon Steel Rebar
Carbon steel rebar, also known simply as steel rebar or black rebar, is the most commonly used type of reinforcing bar in construction. It is made from carbon steel, a material known for its high tensile strength and durability. The primary function of carbon steel rebar is to reinforce concrete structures by providing the tensile strength that concrete lacks.
Key Characteristics
- Strength: Carbon steel rebar significantly enhances the tensile strength of concrete, making it more capable of withstanding various stresses and loads.
- Ductility: This type of rebar can bend without breaking, which is beneficial during construction and for the overall flexibility of the reinforced structure.
- Bonding: The surface of carbon steel rebar typically features ridges or deformations, improving its bond with concrete and preventing slippage within the structure.
- Cost-Effectiveness: Carbon steel rebar is generally less expensive compared to other types of rebar, making it a cost-effective choice for many construction projects.
Applications
Carbon steel rebar is used in a wide range of construction projects, including:
- Building foundations
- Beams and columns
- Bridges and highways
- Retaining walls
- Slabs and pavements
Limitations
While carbon steel rebar is versatile and widely used, it is susceptible to corrosion when exposed to moisture and chemicals. This can compromise the integrity of the reinforced concrete over time. To mitigate this issue, protective measures such as coatings or using corrosion-resistant types of rebar (like epoxy-coated or stainless steel rebar) are often employed in environments prone to corrosion.
Stainless Steel Rebar
Stainless steel rebar is a type of reinforcing bar made from stainless steel, known for its excellent corrosion resistance, strength, and durability. It is used in concrete structures where enhanced durability and resistance to harsh environments are required.
Key Characteristics
- Corrosion Resistance: The primary advantage of stainless steel rebar is its exceptional resistance to corrosion. It is highly effective in environments exposed to moisture, chlorides, and chemicals, such as coastal areas or industrial sites.
- Strength: Stainless steel rebar offers high tensile strength, which contributes to the overall strength and longevity of the reinforced concrete structures.
- Ductility: Similar to carbon steel rebar, stainless steel rebar can bend without breaking, providing flexibility during construction and enhancing the structural resilience.
- Longevity: Structures reinforced with stainless steel rebar have a longer lifespan due to the material's resistance to corrosion and wear, reducing the need for frequent repairs or replacements.
- Cost: While more expensive upfront compared to carbon steel rebar, the long-term benefits, including reduced maintenance and extended lifespan, can offset the initial costs.
Applications
Stainless steel rebar is used in various construction projects where enhanced durability and resistance to corrosive environments are critical, including:
- Coastal and marine structures (piers, seawalls, and bridges)
- Chemical plants and industrial facilities
- Infrastructure exposed to de-icing salts (roadways, tunnels, and parking garages)
- Water treatment plants
- Historical building restorations
Limitations
The main limitation of stainless steel rebar is its higher initial cost compared to carbon steel rebar. However, in environments where corrosion is a significant concern, the investment can be justified by the extended lifespan and reduced maintenance costs of the reinforced structure.
Galvanized Rebar
Galvanized rebar is a type of reinforcing bar that has been coated with a layer of zinc to protect it from corrosion. This zinc coating acts as a barrier, preventing moisture and chemicals from reaching the steel underneath and causing rust.
Key Characteristics
- Corrosion Resistance: The zinc coating on galvanized rebar provides excellent protection against corrosion, especially in environments where concrete structures are exposed to moisture, chlorides, and other corrosive elements.
- Durability: By protecting the underlying steel, galvanized rebar extends the lifespan of concrete structures, reducing the likelihood of premature deterioration due to rust.
- Strength: Galvanized rebar maintains the high tensile strength of carbon steel rebar while offering added protection against environmental factors.
- Bonding: The zinc coating does not significantly affect the bond strength between the rebar and concrete, ensuring that the rebar remains securely embedded within the concrete structure.
- Cost: Although more expensive than uncoated carbon steel rebar, galvanized rebar is generally more affordable than stainless steel rebar, providing a cost-effective solution for enhanced corrosion resistance.
Applications
Galvanized rebar is used in various construction projects where increased durability and resistance to corrosion are needed, including:
- Coastal and marine structures (docks, piers, and seawalls)
- Bridge decks and abutments
- Roadways and tunnels
- Parking garages and ramps
- Water and wastewater treatment plants
- Foundations and retaining walls in corrosive soils
Limitations
While galvanized rebar offers improved corrosion resistance, it is not as corrosion-resistant as stainless steel rebar. The zinc coating can also be damaged during handling and installation if not carefully managed, potentially compromising its protective benefits. Additionally, the initial cost is higher than standard carbon steel rebar, though it is often justified by the extended lifespan and reduced maintenance requirements of the structure.
Fiberglass Rebar
Glass Fiber Reinforced Polymer (GFRP) rebar, also known as fiberglass rebar, is a type of reinforcing bar made from high-strength glass fibers embedded in a polymer resin matrix. This composite material offers several advantages over traditional steel rebar, including superior corrosion resistance and high tensile strength.
Key Characteristics
- Corrosion Resistance: GFRP rebar is inherently resistant to corrosion, making it ideal for use in environments where steel rebar would corrode, such as marine environments, chemical plants, and structures exposed to de-icing salts.
- Lightweight: GFRP rebar is significantly lighter than steel rebar, making it easier to handle and transport on construction sites. Its lightweight nature also reduces the overall weight of concrete structures, potentially lowering construction costs and allowing for easier installation in tight spaces.
- High Strength: Despite its lightweight, GFRP rebar offers high tensile strength, comparable to or even exceeding that of steel rebar. This strength makes it suitable for reinforcing a wide range of concrete structures, including bridges, parking garages, and industrial buildings.
- Non-Conductive: Unlike steel rebar, GFRP rebar is non-conductive, making it suitable for use in applications where electrical conductivity is a concern, such as in proximity to power lines or in structures with sensitive electronic equipment.
- Durability: GFRP rebar is resistant to chemicals, UV radiation, and environmental degradation, ensuring long-term durability and minimal maintenance requirements.
Applications
GFRP rebar is used in a variety of construction projects, including:
- Bridges and highway infrastructure
- Marine structures (piers, docks, and seawalls)
- Chemical plants and industrial facilities
- Parking garages and decks
- Precast concrete elements
- Rehabilitation of existing structures prone to corrosion
Limitations
While fiberglass rebar offers many advantages, it is generally more expensive than steel rebar, which can impact project budgets. Additionally, GFRP rebar may require special installation techniques and hardware due to its different properties compared to steel rebar. Care must also be taken during handling and installation to avoid damage to the rebar's surface or fibers.
Epoxy Coated Rebar
Epoxy coated rebar is a type of reinforcing bar that has been coated with a layer of epoxy resin to protect it from corrosion. This coating acts as a barrier, preventing moisture and chemicals from reaching the steel surface and causing rust.
Key Characteristics
- Corrosion Resistance: The epoxy coating provides excellent protection against corrosion, particularly in environments where steel rebar would be susceptible to rust, such as coastal areas, bridges, and highway infrastructure.
- Durability: Epoxy coated rebar extends the lifespan of concrete structures by preventing corrosion of the underlying steel, reducing the need for maintenance and repairs over time.
- Bonding: The epoxy coating does not significantly affect the bond strength between the rebar and concrete, ensuring that the rebar remains securely embedded within the structure.
- Versatility: Epoxy coated rebar can be used in a wide range of construction projects, including bridges, highways, parking garages, and marine structures, where corrosion resistance is essential.
- Cost-Effectiveness: While typically more expensive than uncoated steel rebar, the long-term benefits of using epoxy coated rebar, including reduced maintenance costs and extended service life, often justify the initial investment.
Applications
Epoxy coated rebar is used in various construction projects where corrosion protection is critical, including:
- Bridges and highway infrastructure
- Parking garages and ramps
- Marine structures (piers, docks, and seawalls)
- Water and wastewater treatment plants
- Industrial facilities
- Rehabilitation of existing structures prone to corrosion
Limitations
Although epoxy coated rebar offers excellent corrosion protection, care must be taken during handling and installation to avoid damaging the epoxy coating, as this can compromise its effectiveness. Additionally, epoxy coated rebar may be more susceptible to damage during construction activities such as cutting and bending compared to uncoated steel rebar.
Welded Wire Fabric (WWF) Rebar
Welded Wire Fabric (WWF) rebar, also known as wire mesh or wire fabric, is a prefabricated reinforcement material composed of interconnected steel wires welded together to form a grid or mesh pattern. This mesh is used to reinforce concrete structures, providing both tensile strength and crack control.
Key Characteristics
- Strength: Welded wire fabric rebar provides tensile strength to concrete structures, helping to distribute loads and resist cracking under stress. It enhances the overall structural integrity and durability of concrete elements.
- Flexibility: WWF rebar is highly flexible and can be easily bent or cut to fit the contours of complex shapes or irregular forms, making it suitable for a wide range of construction applications.
- Ease of Installation: As a prefabricated material, welded wire fabric rebar is quick and easy to install compared to traditional loose rebar. It comes in rolls or sheets, allowing for efficient handling and placement on construction sites.
- Uniformity: The grid pattern of WWF rebar ensures uniform distribution of reinforcement throughout the concrete, minimizing the risk of localized weak points and enhancing structural performance.
- Cost-Effectiveness: Welded wire fabric rebar is often more cost-effective than traditional loose rebar, particularly for large-scale projects or applications where extensive reinforcement is required.
Applications
Welded wire fabric rebar is used in a variety of construction projects, including:
- Slabs and pavements
- Walls and columns
- Footings and foundations
- Bridge decks and highway pavements
- Precast concrete elements
- Reinforcement of masonry structures
Limitations
While welded wire fabric rebar offers numerous advantages, it may not be suitable for all applications, particularly those requiring precise placement of reinforcement or where complex shapes or configurations are involved. Additionally, WWF rebar may have limitations in terms of achieving specific design requirements compared to traditional loose rebar.
Expanded Metal Rebar
Expanded metal rebar, also known as expanded metal mesh, is a type of reinforcing material made from a sheet of metal that has been slit and stretched to form a pattern of diamond-shaped openings. This mesh is used to reinforce concrete structures, providing strength, support, and crack control.
Key Characteristics
- Strength: Expanded metal rebar offers high tensile strength, enhancing the load-bearing capacity and structural integrity of concrete elements. It helps distribute loads and resist cracking under stress, improving the overall durability of the structure.
- Flexibility: Expanded metal rebar is flexible and can be easily bent or cut to fit the contours of complex shapes or irregular forms, making it adaptable to various construction applications.
- Openings: The diamond-shaped openings in expanded metal rebar allow for improved bond with concrete, ensuring effective transfer of stresses between the reinforcement and the concrete matrix.
- Surface Area: The large surface area of expanded metal rebar provides enhanced bonding with concrete, promoting adhesion and reducing the risk of delamination or separation between the reinforcement and the concrete.
- Cost-Effectiveness: Expanded metal rebar is often more cost-effective than traditional steel rebar, particularly for large-scale projects or applications where extensive reinforcement is required. Its efficient manufacturing process and lightweight nature contribute to its affordability.
Applications
Expanded metal rebar is used in various construction projects, including:
- Slabs and pavements
- Walls and partitions
- Bridge decks and highway pavements
- Industrial flooring and platforms
- Reinforcement of precast concrete elements
- Suspended ceilings and decorative applications
Limitations
While expanded metal rebar offers numerous advantages, it may not be suitable for all applications, particularly those requiring precise placement of reinforcement or where high levels of corrosion resistance are needed. Additionally, expanded metal rebar may have limitations in terms of achieving specific design requirements compared to traditional steel rebar.
Conclusion
Understanding rebar is crucial for anyone involved in construction or engineering. This guide has provided an overview of what rebar is, how to interpret rebar size charts from different regions, and the significance of rebar grades.
We also explored the various types of rebar, each suited for specific applications. With this knowledge, you can confidently select the right rebar for your projects, ensuring they are strong, durable, and reliable.